Hook-Up & Start Up
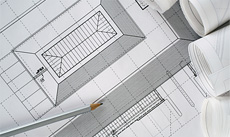
Our engineering Project Team works with customers to understand their technological, schedule and budget requirements, and develops optimized designs for the manufacturing processes. Our professionals provide superior engineering support for upgrades of an existing base building facility while ensuring that safety, quality, maintainability and constructability are achieved.
Space planning and design for tool fit-up and hook-ups are provided by our engineers avoiding inefficient space utilization, minimizing total cost-per-tool installation, as well as addressing personnel safety.
During the fit-up phase our engineers participate in the commissioning of a facility building system which is installed per a tool manufacturer's specifications prior to the hook-up stage. Tool hook-up begins with the development of specific methodology for tool move-in, addressing floor load, spacing, clearances and all specific installation requirements. Tool hook-ups range from base building HVAC mechanical systems and electrical installations to industrial drainage systems, inert gases, and hazardous production material (HPM) gases, HPM gas cabinets or hazardous and combustible fluids.
The commissioning process for any tool starts with the tool sign-off procedure employing various checklists that guide each of the participants through a review of the tool installation. It allows for independent perusal of the work by each responsible group to access the integrity, quality assurance, safety and functionally of the installation based on acceptable risk inherent in any complex undertaking. The tool sign-off forms are used by all parties participating in the commissioning (of the installation) process for achieving, verifying and documenting the performance of the system to meet the operational needs, the design intent documentation and the owner's functional criteria including preparation of operations personnel.